News:
Eddy Current Testing
Eddy current testing is used to detect surface and near-surface flaws in conductive materials.
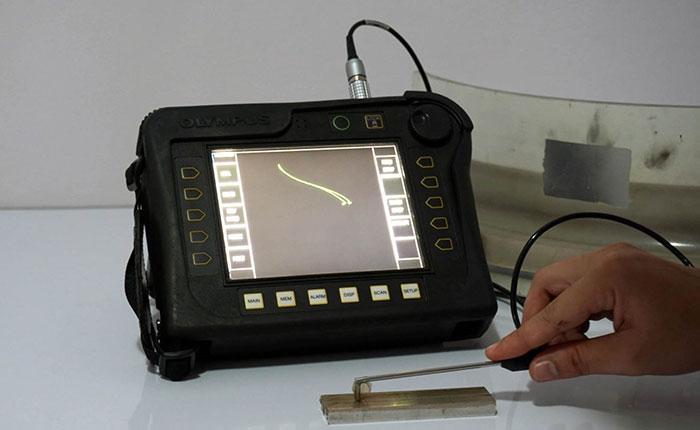
This non-destructive testing technique is non-hazardous and commonly used in industries such as aerospace, rail, automotive, marine and manufacturing. One of the major advantages of eddy current testing is that inspection requires minimum preparation as there is no need to remove surface paint or coating. This makes it suitable for inspecting painted structures, parts and components.
Eddy current testing equipment is highly portable, reliable and can detect very small cracks. Results are instant, ideal for on-site testing on-site and plant inspections. Flaws can be reported immediately to site and operation managers, allowing for quicker decision making. In addition, the portability of equipment means that we can inspect equipment or assets that are difficult to access, and test complex shapes and sizes.
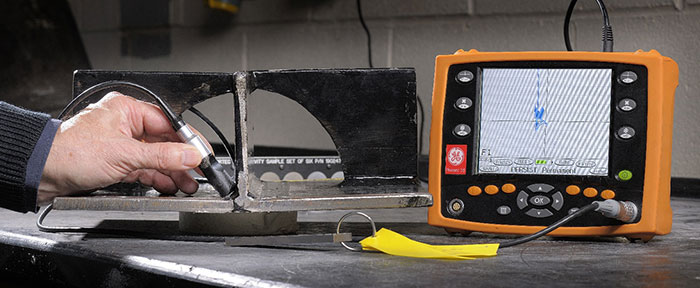
Eddy current testing uses electromagnetic induction to detect defects in both ferrous and non-ferrous materials by inducing an eddy current field in the specimen under test. A variety of inspections can be performed with eddy current testing and it is typically used for surface and near-surface flaw detection, metal and coating thickness measurement, and metal sorting by grade and hardness.
Our inspectors are highly experienced in performing this non-destructive technique and are PCN or ASNT Levels 2 and 3 qualified in eddy current testing.
Aria Azmoon Sanat Co. is committed to offering Total Quality Assurance and ensuring plant inspections meet deadlines and are carried out safely and efficiently. Maintenance schedules are co-ordinated to ensure minimum disruption to your business activities and planned with an optimum level of NDT personnel to achieve the requisite inspection within the shortest possible time.

Eddy current testing on tubes
Eddy current testing on tubes in heat exchangers, condensers, air conditioning and air coolers, requires specialist equipment and technical expertise. Aria Azmoon sanat NDT inspectors can perform this specialist advanced method.
Eddy current testing is a non-destructive testing method widely used to examine tubing in heat exchangers, steam generators, condensers, air coolers and feed water heaters.
Eddy current testing of tubes is an effective way of assessing the condition and lifespan of tubes, particularly in the power generation, petrochemical, chemical, fertilizer and air conditioning industries. The technique is applied to detect corrosion, pitting, cracks, erosion and other changes to both the tube’s interior and exterior surfaces.

It is a high-speed inspection method and one of the major advantages is that it can be performed through paint and coatings. The technique is only suitable for non-ferrous material such as stainless steel, copper and titanium. We also perform remote field and magnetic biased eddy current testing on carbon tubing.
Eddy current testing uses electromagnetic induction to identify defects in tubing. A probe is inserted into the tube and pushed through the entire length of the tube. Eddy currents are generated by the electromagnetic coils in the probe and monitored simultaneously by measuring probe electrical impedance. The information revealed by the probe will detail the tube defects. The scanning data will be recorded by the software and kept us as a backup for future reference.
A benefit of eddy current testing is that detection of defects is instant, and can be reported immediately to site or operation managers.
Eddy current testing of tubes is highly specialized, requiring expertise and specialist equipment. Aria Azmoon sanat non-destructive testing inspectors are PCN, ASNT Level II or III qualified in eddy current testing, and have years of experience in performing this technique on tubing. Our inspectors’ expertise will ensure you have an accurate assessment of the condition and remaining useful life of your tubing so that you have the information to make decisions regarding the asset integrity management of your tubes.
Aria Azmoon Sanat extensive experience in eddy current tube testing for various industries means that we understand the need for quick turnaround times during outages. You can have the Total Quality Assurance that outage schedules will be met with our eddy current inspections.
Detect the Smallest Flaws with Eddy-Current Testing
If you need to detect flaws in conductive material, eddy-current testing is one of the most reliable ways, giving you the capability to detect very small cracks in or near the material’s surface.
We have numerous years of experience with this type of conductive material inspection and are able to set up individual testing parameters to best meet your needs.
Benefits of Our Eddy-Current Testing Services
- Fast results with a portable device.
- A lead against the competition with a neutral audit seal.
- Reduced risk of company liability with documented safety standards.
- Fast audit times and our long-standing experience.
- Demonstrating your high-quality standards.
- Compliance with local government and legal requirements.
Eddy-Current Testing Approach
A circular coil carrying current is placed in proximity to the electrically conductive test specimen. The alternating current in the coil generates a changing magnetic field, which interacts with the test specimen and generates eddy-current.
Variations in the phase and magnitude of these eddy-currents can be monitored using a second “search” coil or by measuring changes to the current flowing in the primary “excitation” coil.
The machine can be set up to accept parts within a certain range of signal interpretation. This is done by utilizing a series of known good samples that are run through the coils in order to calibrate the machine. The different pieces are then tested. Parts that fall outside this range are rejected, usually with a red indicator light.
More Information on Eddy-Current Testing
Eddy-current testing uses electromagnetic induction to detect flaws in conductive materials. It can detect very small cracks in or near the surface of the material.
Parts capable of inducing current are put in contact or near a probe that emits electromagnetic currents through the part. The probe also looks for changes in how the current travels through the part. It picks up the changes and shows the irregular flow. This process can detect slight changes in the piece being inspected. The changes may be due to hardness difference, changes in material, or a void or crack in the part.
The material surface needs minimal preparation, and physically complex geometries can be investigated. It is also useful for making electrical conductivity and coating thickness measurements.
Eddy-current testing equipment is relatively expensive and complex in nature, so having experienced personnel and quality equipment is a must.