بازرسی دوره ای مخازن تحت فشار (API 510)
ثبت نام دوره
نوع دوره | تاریخ شروع | تاریخ پایان | ساعت شروع | ساعت پایان | شهریه (ریال) | ثبت نام |
---|---|---|---|---|---|---|
آنلاین | 1404-03-20 | 1404-03-29 | 17:00 | 20:00 | 120,000,000 | ثبت نام |
محتوای دوره بازرسي مخازن تحت فشار در دوره بهره برداري طبق API 510
- تعیین حداقل ضخامت لازم، تعیین میزان رشد خوردگی و تعیین عمر باقیمانده مخازن تحت فشار،
- معیارهای پذیرش حفره ها (Pitting) ، معیار پذیرش انواع خوردگی ها،
- الزامات مرتبط به انجام عملیات تنش زدایی در زمان تعمیرات بر روی مخازن تحت فشار تنش زدایی شده (در زمان ساخت)
- الزامات مربوط به استفاده از مخازن تحت فشار در شرایط کاهش ضخامت بیش از حد مجاز،
- الزامات مربوط به تعمیرات به روش Build-up ، الزامات مربوط به جلوگیری از شکست ترد غیر منتظره،
- معیارهای پذیرش عیوب جوشکاری در زمان تعمیرات،
- محاسبه MAWP و تعیین فواصل بازرسی براساس آن،
- الزامات مربوط به بازرسی مخازن تحت فشار عایق دار،
- الزامات مربوط به تعمیرات موقت و دائم بر روی مخازن تحت فشار،
- الزامات مربوط به بازرسی شیرهای اطمینان و تعیین روش و فواصل بازرسی های آن،
- الزامات مربوط به عملیات جوشکاری بر روی مخازن تحت فشار،
- الزامات مربوط به بازرسی متریال های مورد استفاده در تعمیرات مخازن تحت فشار
- الزامات مربوط به تغییر شرایط طراحی (Alteration & Re_ rating) و (تغییر دما، فشار و یا سرویس)
- رفع اشكال، مرور مباحث گذشته و آزمون
مخاطبین دوره بازرسي مخازن تحت فشار در دوره بهره برداري طبق API 510
تکنیسینها و مهندسین واحدهای بازرسی فنی و کنترل کیفیت (QC ) ، واحدهای تعمیرات ، کارشناسان دستگاه نظارت که در بازرسي سایتهای عملیاتی و فرآیندی در صنايع نفت ، گاز ، پتروشيمي ، پالايشگاهي و نيروگاهي فعاليت دارند ، دانشجویان و کلیه افراد علاقمند و مرتبط با بازرسی مخازن تحت فشار در دوره بهره برداري
تواناييها پس از طی دوره بازرسي مخازن تحت فشار در دوره بهره برداری طبق API 510 در شرکت آریا آزمون صنعت
- آگاهی کامل از الزامات مربوط به عملیات جوشکاری تعمیری بر روی مخازن تحت فشار
- آگاهی از معیارهای پذیرش عیوب جوشکاری در زمان تعمیرات
- تعیین حداقل ضخامت لازم، تعیین میزان رشد خوردگی و تعیین عمر باقیمانده مخازن تحت فشار
- آگاهی از الزامات مربوط به تعمیرات موقت و دائم بر روی مخازن تحت فشار

گواهینامه های قابل صدور پس از طی دوره بازرسي مخازن تحت فشار در دوره بهره برداری طبق API 510
- گواهینامه معتبر پایان دوره API 510 Pressure Vessel Inspector از طرف موسسه آریا آزمون صنعت مورد تایید سازمان های فوق
- امکان صدور گواهینامه بازرس مخازن تحت فشار در دوره بهره برداری از طرف سازمان آموزش فنی و حرفه ای کشور
پیش نیاز دوره بازرسي مخازن تحت فشار در دوره بهره برداری طبق API 510
دارا بودن تحصیلات حداقل فوق دیپلم در یکی از رشته های مهندسی ، آشنایی با اصول بازرسی جوش و آزمایشات غیرمخرب (NDT ) و دارا بودن سابقه کار مرتبط و توانایی خواندن و درک متون انگلیسی مرتبط
مزایای دوره بازرسي مخازن تحت فشار در دوره بهره برداری طبق API 510 برای افرادی که قصد مهاجرت دارند
گواهینامه دوره بازرسي مخازن تحت فشار در زمان بهره برداری موسسه آریا آزمون صنعت با توجه به اعتبارات سازمانی این موسسه و اینکه دوره بر اساس الزامات استاندارد معتبر API 510 برگزار می شود ، نیاز به ترجمه نداشته و مستقیما در بسیاری از کشورهای جهان، معتبر و قابل استفاده می باشد. لذا بسیاری از افرادی که قصد مهاجرت به کشور های مختلف را دارند به منظور کسب دانش فنی و مهارت در حوزه بازرسی فنی و نیز اخذ یک گواهینامه معتبر، به موسسه آریا آزمون صنعت مراجعه می کنند.
ضمنا مدارکی که فرد پیرو گذراندن دوره در این موسسه، از سازمان آموزش فنی و حرفه ای کشور دریافت میکند، پس ازترجمه و با توجه به دولتی بودن سازمان فنی و حرفه ای، بسیار معتبر بوده و به عنوان یک مدرک قابل ارایه در پروسه مهاجرت استفاده می شود.
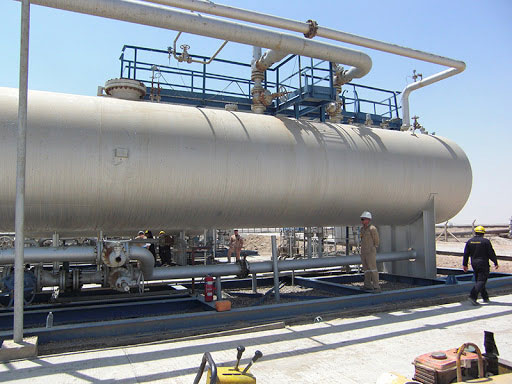
آشنایی با بازرسي مخازن تحت فشار
وجود ظروف، دیگ ها و مخازن تحت فشار در صنایع مختلف به دلیل کاربرد فراوان این تجهیزات، کارایی مناسب آنها و ... بسیار حایز اهمیت می باشد. تعریف مخازن تحت فشار را می توان بطور کلی در این جمله خلاصه نمود، به کلیه مخازنی که فشار درون آنها بیشتر از 1 اتمسفر باشد مخزن تحت فشار می گویند. این مخازن ممکن است بطری نوشابه و یا دیگ بخار یک کارخانه پالایش نفت باشد. لازم به ذکر است هر چه فشار درون این مخازن بالاتر باشد خطرهای ناشی از کار با این دستگاه ها نیز بیشتر خواهد بود. به همین دلیل بسیار مهم، پیشنهاد می گردد بازرسی دوره ای با زمان بندی استاندارد از مخازن با اولویت بالا مورد توجه بازرسان و متخصصان قرار گیرد. در این بحث سعی می شود تا نکاتی مهم از زمان سفارش و ساخت و تحویل و نصب مخازن در سایت کارخانه مورد بررسی قرار گیرد. بهترین و مناسب ترین ابزار برای بررسی چک لیست می باشد و لازم به ذکر است کسب دانش در ارتباط با تهیه چک لیست و یا استفاده کاربردی از چک لیست بسیار مهم است.
در بازرسی از مخازن، فرآیند بازرسی را می توان به 3 بخش زیر تقسیم بندی نمود:
- 1. بازرسی پیش از ساخت
- 2. بازرسی حین ساخت
- 3. بازرسی نهایی
یادآوری: لازم به ذکر می باشد کلیه مراحل بازرسی از اهمیت خاصی برخوردار است و کوچک ترین کوتاهی و یا نقص در این موضوع می تواند منجر به بروز حادثه ای فاجعه آمیز گردد. اهمیت بازرسی از این لحاظ مورد اهمیت می باشد که کلیه مراحل یک فرآیند هم از بابت بازرسی در مراحل مختلف و هم بازرسی های دوره ای در حین بهره برداری در عملکرد صحیح دستگاه و همچنین پیشگیری از حوادث، می تواند با رفتار حرفه ای یک بازرس جهت انجام عملیات بازرسی دقیق و مناسب تاثیرگذار باشد.
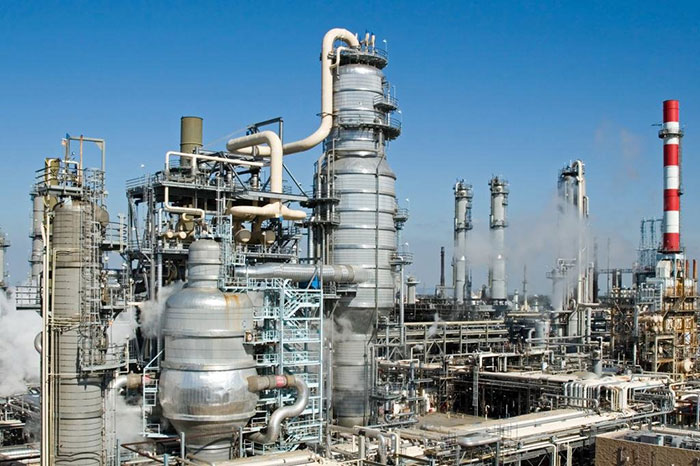
1- بازرسی پیش از ساخت
در این مرحله یک بازرس باید مراحل مختلفی را مورد بررسی قرار دهد. مهمترین این اقدامات را می توان اینگونه در نظر گرفت که بازرس در ابتدا باید وضعیت کارخانه سازنده از لحاظ در اختیار داشتن تجهیزات متناسب برای ساخت انواع جرثقیل ها، تجهیزات جوشکاری، نیروی انسانی مناسب و ... و تجهیزات مورد نیاز جهت کنترل کیفی مراحل ساخت، مواد و محصول و در مجموع توانمندی کارخانه سازنده را مورد بررسی قرار دهد که حتی این اقدامات شامل چک نمودن سیستم مدیریت کیفیت و سایر استانداردهای مورد نیاز نیز می باشد.
بازرس قبل از شروع کار باید در جلسه پیش از شروع بازرسی شرکت و نظرات خود را در رابطه با شرایط کلی بازرسی، نحوه کنترل کیفی و ... ارائه و صورتجلسه را امضاء و با حضور افراد مرتبط تایید نماید. پس از آن مشاهده و تایید گواهینامه فنی مواد شامل انواع ورق های مورد استفاده، لوله ها، فلنج ها، الکترود، رنگ و ... و بازرسی از مواد مورد استفاده و تایید و در صورت نیاز تست از جوشکاران و تایید گروه عملیات تست غیر مخرب بازرسی گواهینامه های کالیبراسیون دستگاه های مورد استفاده از قبیل دستگاه های جوشکاری، گرم کن الکترود، تجهیزات ماشین کاری و ... ، مشاهده و تایید گواهی نامه های کالیبراسیون دستگاه های مورد استفاده گروه کنترل کیفیت و همچنین مرور و تایید دستورالعمل های NDT، PQR، WPS، تست های هیدرواستاتیک (یا نیوماتیک)، Hardness, PMI، دستورالعمل های تنش زدایی، رنگ و سند بلاست از جمله مراحلی می باشد که یک بازرس مجرب باید به آنها توجه و با توجه به اطلاعات خود آنها را مورد بررسی و تایید قرار دهد.
بازرسی قبل از ساخت به زبان خلاصه
- 1- بررسی وضعیت عمومی کارخانه سازنده از لحاظ تیم کاری، تجهیزات و سایر موارد
- 2- دارا بودن سیستم مدیریت و استانداردهای مورد نیاز در کارخانه سازنده
- 3- تشکیل جلسات قبل از شروع بازرسی (Pre – inspection meeting)
- 4- دارا بودن گواهینامه موارد مورد استفاده و مصرفی(Material Certification)
- 5- تایید جوشکار
- 6- تایید گروه تست غیر مخرب
- 7- تایید گواهینامه دستگاه های مورد استفاده
- 8- تایید دستورالعمل های کاری
2- بازرسی حین ساخت
در این مرحله از بازرسی که پس از اتمام مرحله قبل صورت می گیرد بازرسی در حین ساخت و نظارت بر روند ساخت و تست ها باید انجام گردد. بازرسی از روند ساخت ورق ها، علامت گذاری، آماده سازی لبه ها، بررسی جوش، نظارت بر تست های غیر مخرب، رول کردن و مونتاژ ورق، نظارت بر انجام انواع تست ها و ... از مواردی می باشد که بازرسی در انجام عملیات بازرسی باید به آن توجه نماید.
بازرسی حین ساخت به زبان خلاصه
- 1- بازرسی ابعادی علامت گذاری ها (Marking) پیش از برش ورق ها
- 2- نظارت بر انتقال Stamp (اطلاعات شناسایی مواد) به قسمت های مختلف ورق قبل از برش (قسمت های تحت فشار)
- 3- نظارت و کنترل بر آماده سازی لبه های ورق (پخ زنی ها) طبق WPS و نقشه ها
- 4- بازرسی چشمی و ابعادی ورق های برش خورده
- 5- نظارت بر انجام تست های غیر مخرب PT (تست مایعات نافذ) بر روی لبه های ورق ها برای ضخامت های بالای cm۵۰ (در صورت نیاز)
- 6- کنترل بر رول کردن اولیه (نورد) ورق ها طبق نقشه ها
- 7- نظارت بر مونتاژ ورق و جوشکاری درز طولی آن طبق WPS و نقشه
- 8- بازرسی چشمی جوش
- 9- نظارت بر رول کردن ثانویه ورق ها
- 10- بازرسی ورق ها از لحاظ بیضوی و Roundness (گردی)، ضخامت و ابعاد طبق نقشه و استاندارد
- 11- نظارت بر آزمون غیر مخرب RT و PT جوش طولی
- 12- نظارت بر مونتاژ و جوشکاری درزهای محیطی طبق نقشه وWPS
- 13- بازرسی چشمی جوش
- 14- نظارت بر آزمون غیر مخرب RT و PT جوش محیطی
- 15- نظارت و کنترل علامت گذاری (Marking) محل نازل ها روی شل (Shell) پیش از برش
- 16- نظارت و کنترل ابعادی هدها (عدسی ها و ...) بعد از عملیات Forming از لحاظ ضخامت و انحنای مورد نیاز طبق نقشه
- 17- نظارت بر انجام آزمون غیر مخرب MT بر روی سطح خارجی ناکل (Knuckle) عدسی ها
- 18- نظارت بر مونتاژ و جوشکاری اولین هد به Shell
- 19- بازرسی چشمی جوش
- 20- نظارت بر انجام آزمون های PT و RT جوش عدسی به Shell
- 21- نظارت بر مونتاژ جوشکاری فلنج به نازل
- 22- بازرسی چشمی جوش
- 23- نظارت بر انجام آزمون RT جهت جوش فلنج به نازل (در صورت امکان)
- 24- نظارت بر مونتاژ و جوشکاری نازل به شل و یا عدسی
- 25- بازرسی چشمی جوش
- 26- نظارت بر انجام آزمون UT جوشکاری نازل به شل و یا عدسی
- 27- مونتاژ و جوشکاری Reinforcing Pad (ورق تقویتی)
- 28- نظارت بر انجام تست نشتی هوا (Air Leak Test) با استفاده از آب و صابون جهت ورق تقویتی
- 29- کنترل بر مونتاژ و جوشکاری عدسی دوم به شل/ بازرسی چشمی جوش/ RT عدسی دوم به شل
- 30- کنترل چشمی و ابعادی ساخت Leg/Saddle/Skirt
- 31- بازرسی چشمی جوش Leg/Saddle/Skirt به مخزن
- 32- نظارت بر انجام آزمون های PT یا MT جوش Skirt به عدسی/ Saddle یا Leg به مخزن
- 33- نظارت بر مونتاژ و جوشکاری قسمت های خارجی و داخلی مخزن (کلیپ های نردبان، پلت فرم و …)
- 34- نظارت بر انجام آزمون های PT یا MT جهت قسمت های داخلی و خارجی
- 35- تست PMI و یا Ferrite Content Test (در صورت نیاز)
- 36- بازرسی نهایی ابعادی و چشمی مخزن
- 37- نظارت بر تنش گیری (عملیات حرارتی پس از جوشکاری) و کنترل چارت PWHT
- 38- نظارت بر انجام آزمون سختی سنجی (Hardness) و Production Test
- 39- نظارت بر تمیز بودن و تمیزکاری سطوح داخلی مخزن
- 40- نظارت بر انجام تست فشار Hydro test
- 41- بازرسی نهایی ابعادی و چشمی بعد از فشار
- 42- نظارت بر سند بلاست و رنگ مخزن
- 43- نظارت بر ساخت و نصب لوحه شناسایی (Name Plate)
3- بازرسی نهایی
در این قسمت از بازرسی که جهت اتمام ساخت و تحویل گرفتن کار انجام می گردد بر بازرسی و کنترل نهایی کلیه قسمت ها تجهیزات و همچنین مدارک نهایی و شرایط بسته بندی و ارسال آن تا سایت دلالت می نماید. که بطور خلاصه به شرح ذیل می باشد.
بازرسی نهایی به زبان خلاصه
- 1- بازنگری و کنترل مدارک نهایی سازنده (MDR)
- 2- بازرسی بسته بندی و علامت گذاری های روی مخزن
- 3- صدور گواهینامه ترخیص مخزن
- 4- نظارت بر بارگیری مخزن
- 5- صدور گواهینامه ارسال مخزن
همانطور که ذکر گردید بازرسی در مراحل مختلف بسیار مهم می باشد و در این راستا در هنگام بهره برداری چک نمودن و کنترل تجهیزات جهت افزایش راندمان کاری و همچنین پیشگیری از حوادث نیز از اهمیت فوقالعاده ای برخوردار می باشد. و مهمترین عامل در این جریان در هنگام کار و استفاده از تجهیزات، خوردگی می باشد که می تواند ناشی از عوامل مختلفی باشد. علاوه بر بازرسی خوردگی، بازرسی ترک، بازرسی ایمنی، بازرسی از لبه های جوش، تست فشار و ... از مواردی می باشند که یک بازرس باید با دقت به آنها توجه نماید و از کوچک ترین اشکال حتی جزئی هم چشم پوشی ننماید.
مخازن تحت فشار دارای اجزای مختلفی هستند که هر بخش از نظر ابعادی حداقل الزامات زیر را باید دارا باشد. البته در همه حالت ها می بایست مقدار خوردگی وسایش مجاز نیز به حداقل ضخامت ها اضافه شوند. در صورتیکه در محاسبات بر مبنای تحلیل تنش، ضخامت ها از مقادیر ذیل کمتر شوند. مبنا را باید حداقل در نظر گرفت
- 1) ضخامت mixer ها و یا قطعات چرخان ازجمله پره های آنها حداقل برابر با 1.5mm به عنوان ضخامت هشدار لحاظ شود.
- 2) حداقل ضخامت مورد نیاز برای بدنه و عدسی بویلر ها برابر با 6 میلیمتر می باشد.
- 3) حداقل ضخامت مورد نیاز برای سیستم های هوای فشرده(Compress Air) ، سرویس های بخار، سرویس های آب( در صورتیکه از متریال فهرست شده انتخاب شده باشند) برابر با 2.5mm می باشد.
- 4) موارد مذکور برای سرویس های سمی (Lethal) و تیوب های حاوی فین نباید استفاده شوند.
- 5) قطر خارجی برای اجزای قطعات قید شده در بند3 حداقل 10 میلیمتر و حداکثر 38 میلیمتر لحاظ شود.
- 6) بعد از محاسبه حداقل ضخامت مورد نیاز برای ورق میزان مجاز ی که سازنده مجاز است داشته باشد 6 درصد ضخامت یا 0.3 میلیمتر ( هر کدام که کمتر بودند) می باشد.برای لوله هم این موضوع بایستی با توجه به مقداری که در اسپک های ساخت لوله عنوان شده است رعایت گردد.(12.5 % Thickness)
بیشتر بدانید
ثبت نام دوره
نوع دوره | تاریخ شروع | تاریخ پایان | ساعت شروع | ساعت پایان | شهریه (ریال) | ثبت نام |
---|---|---|---|---|---|---|
آنلاین | 1404-03-20 | 1404-03-29 | 17:00 | 20:00 | 120,000,000 | ثبت نام |